When choosing between rubber and steel tracks for your machine, the decision is based on a few important factors. We often get asked, “Which is better?” The answer isn’t simple, as both options have their advantages depending on the situation.
What is your machine currently fitted with?
A good starting point is to consider your current setup. If your machine is running smoothly and you’re getting good wear life from your rubber or steel tracks, there’s little need to make a change. Converting from one to the other can sometimes be tricky, as different tracks require specific adjustments. For example, steel and rubber track systems often have different tension settings, sprockets, and rollers, so changing could lead to problems like de-tracking or accelerated wear if not done correctly.
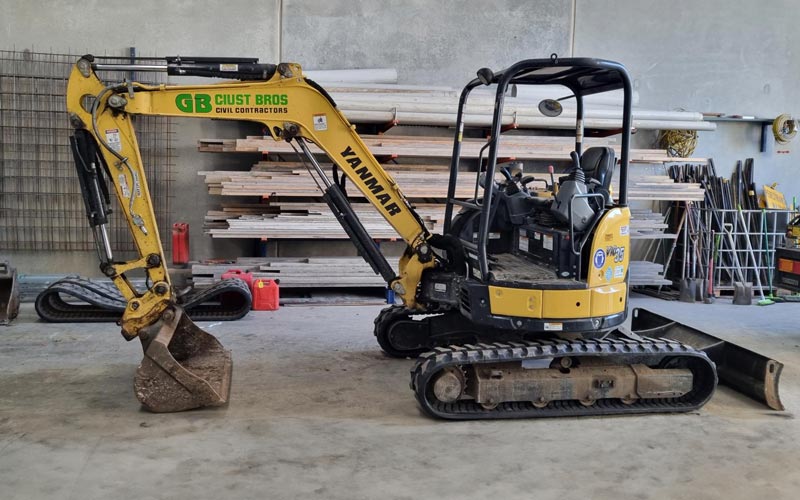
What is the application?
Generally, steel tracks perform better in rough, rocky, or demolition environments. They are also advantageous in steep or hilly terrains where rubber tracks may struggle with de-tracking. In contrast, rubber tracks are ideal for general applications, particularly on paved or grassed surfaces. For mini excavators under 4 tonnes, rubber tracks are usually more cost-effective. Additionally, if you need steel tracks for tougher conditions but work on paved surfaces, there are rubber track pads available to fit most machines.
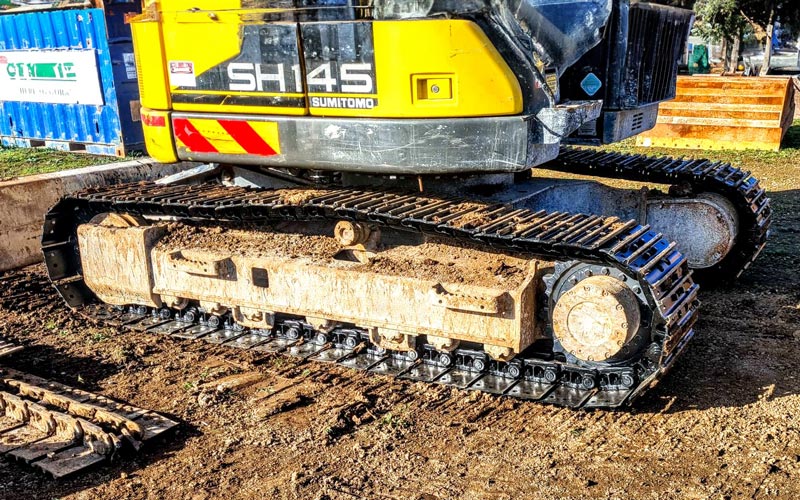
How much tracking does your machine do?
In high tracking environments, where the machine spends more than 40% of its operating time moving, rubber tracks typically offer better wear resistance compared to steel. Steel tracks, particularly those with dry pin assemblies, tend to wear faster under these conditions.
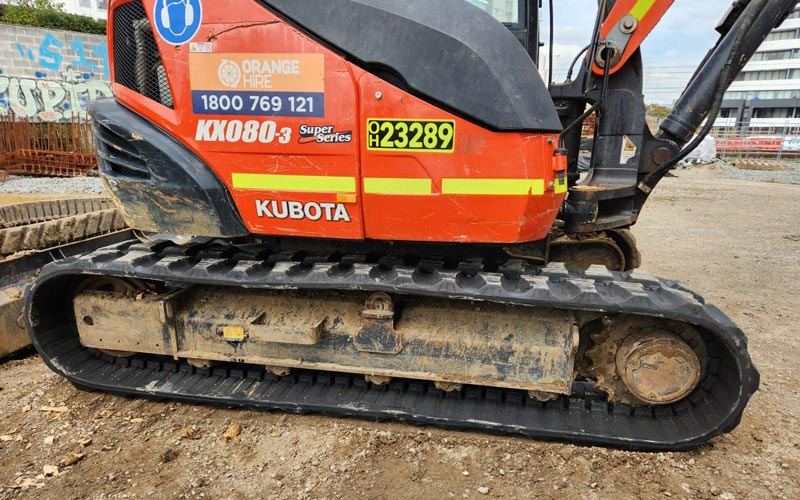
When in doubt, ask!
If you’re unsure which track type is best for your machine and application, don’t hesitate to contact us. We’re here to offer advice to help you make the right choice. 1300 65 11 43